張智峰,溫小萍
(河南理工大學(xué)機(jī)械與動(dòng)力工程學(xué)院,河南焦作454003)
摘要:該文主要針對氫氣爆燃條件下安全性進(jìn)行仿真研究,通過數(shù)值仿真獲得不同工況下發(fā)生氫氣爆燃時(shí)安全殼內(nèi)壓力場、溫度場的空間分布與時(shí)間演化特征,獲得氫氣發(fā)生爆燃時(shí)作用于安全殼內(nèi)壁及安全殼內(nèi)完整、可信的壓力、溫度載荷數(shù)據(jù),從而為安全殼及設(shè)備的力學(xué)響應(yīng)分析提供輸入?yún)?shù)。模擬結(jié)果表明,在安全殼內(nèi)氫氣爆燃爆轟所產(chǎn)生高溫和高壓的影響下,安全殼結(jié)構(gòu)的最大變形為95.274m,最大應(yīng)力約為2.6E+11Pa,遠(yuǎn)大于安全殼所用結(jié)構(gòu)鋼材料的屈服極限,安全殼發(fā)生塑性變形,結(jié)構(gòu)遭到根本性的破壞。
在LOCA(Loss of Coolant Accident)事故工況下,鋯合金包殼與水或水蒸氣發(fā)生鋯水反應(yīng)而產(chǎn)生大量氫氣,導(dǎo)致在產(chǎn)生源附近或者與安全殼內(nèi)空氣混合后可能發(fā)生燃燒、爆燃或爆炸[1-2]。在氫氣產(chǎn)生源附近區(qū)域,如果有點(diǎn)火源和足夠的氧氣,氫氣將會(huì)燃燒并且產(chǎn)生穩(wěn)定的火焰,稱為擴(kuò)散燃燒。這種燃燒所產(chǎn)生的熱量和壓力峰值較小,通常不會(huì)對安全殼完整性構(gòu)成威脅。在釋放源附近沒有發(fā)生燃燒的氫氣,將與安全殼內(nèi)的水蒸氣、空氣混合,并且在安全殼隔間傳輸,導(dǎo)致安全殼內(nèi)整體或某些局部的氫氣濃度升高。當(dāng)安全殼內(nèi)的氫氣濃度達(dá)到一定比例后,在適合的外界條件下(例如溫度、壓力、氧氣濃度等),這些混合氣體將發(fā)生爆燃,并可能由此轉(zhuǎn)變成爆炸,在極短時(shí)間內(nèi)形成很高的壓力峰值。如果未能及時(shí)采取有效的氫氣緩解措施,氫氣在安全殼內(nèi)可能發(fā)生局部或整體性的爆燃或爆炸,由此產(chǎn)生的靜態(tài)和動(dòng)態(tài)壓力載荷會(huì)危及安全殼完整性,并影響安全殼內(nèi)安全系統(tǒng)安全功能的有效執(zhí)行[3]。
數(shù)值模擬仿真是一項(xiàng)較為成熟的技術(shù),針對該項(xiàng)目這種核反應(yīng)堆安全殼爆燃等危害性極大,實(shí)驗(yàn)成本極高的事故,具有極強(qiáng)的針對性。但是安全殼內(nèi)部復(fù)雜的幾何結(jié)構(gòu),要實(shí)現(xiàn)物理模型的完全真實(shí)構(gòu)建是極為不現(xiàn)實(shí)的,原因在于現(xiàn)有公開資料中僅僅給出了安全殼的整體尺寸,局部復(fù)雜微小構(gòu)件的幾何尺寸和安裝位置均是未知的。因此,需要根據(jù)流體動(dòng)力學(xué)的基礎(chǔ)理論和實(shí)踐,結(jié)合數(shù)值模擬仿真的需要,對幾何模型做適當(dāng)合理的簡化,可以在確保計(jì)算精度的前提下,一方面簡化幾何模型構(gòu)建難度;另一方面最大程度地降低仿真計(jì)算的工作量。
本文通過數(shù)值仿真獲得不同工況下發(fā)生氫氣爆燃時(shí)安全殼內(nèi)壓力場、溫度場的空間分布與時(shí)間演化特征,獲得氫氣發(fā)生爆燃時(shí)作用于安全殼內(nèi)壁及安全殼內(nèi)完整、可信的壓力、溫度載荷數(shù)據(jù),從而為安全殼及設(shè)備的力學(xué)響應(yīng)分析提供輸入?yún)?shù)??紤]到安全殼殼體結(jié)構(gòu)在氫氣爆燃壓力作用下,產(chǎn)生的真實(shí)變形較小,殼體結(jié)構(gòu)的變形不足以對安全殼內(nèi)流場造成明顯的干擾和影響,并且本報(bào)告主要目的是分析氫氣爆燃對安全殼結(jié)構(gòu)性能的影響,因此,在安全殼流固耦合分析過程中,可以假定為流固單向耦合過程,主要分析內(nèi)流場壓力對安全殼位移和應(yīng)力的影響,忽略安全殼變形對內(nèi)流場結(jié)構(gòu)的影響特性。
1研究方法與計(jì)算模型
當(dāng)固體結(jié)構(gòu)變形比較大,導(dǎo)致流體的邊界形貌發(fā)生改變后,流體分布會(huì)發(fā)生明顯的變化,此時(shí)單向耦合不再合適,需要考慮固體變形對流體流動(dòng)的影響。兩者相互作用,最終達(dá)到一個(gè)平衡狀態(tài)。ANSYS WORK-BENCH平臺中雙向流固耦合分析時(shí)[4],fluent計(jì)算流體工況,將耦合面上的壓力數(shù)據(jù)導(dǎo)入到structural中,從而計(jì)算結(jié)構(gòu)的應(yīng)力、應(yīng)變等參數(shù),但認(rèn)為變形量足夠大,足以影響原先的流場形態(tài),故將變形位移回傳給fluent,從而再次計(jì)算在新的固體形狀下的流場數(shù)據(jù),得到耦合面上新的壓力數(shù)據(jù);不斷重復(fù)該過程,直至計(jì)算完成。ANSYS WORKBENCH平臺中雙向流固耦合分析的數(shù)據(jù)流方式如圖1所示。
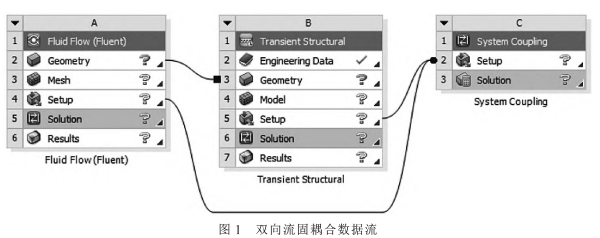
文章主要運(yùn)用湍流流動(dòng)模型、燃燒模型及化學(xué)反應(yīng)模型。其中的湍流燃燒模型,化學(xué)反應(yīng)速率是以反應(yīng)進(jìn)度速率的形式呈現(xiàn)的,反應(yīng)進(jìn)度量描述燃燒反應(yīng)進(jìn)行的程度,并不直接描述所有的化學(xué)反應(yīng)[5]。反應(yīng)進(jìn)度量可以描述反應(yīng)物的反應(yīng)完全程度,是無量綱化的反應(yīng)物組分濃度。對于預(yù)混火焰而言,火焰?zhèn)鞑ニ俣仁菑奈ㄏ蠼嵌让枋龌鹧孢\(yùn)動(dòng)的一個(gè)基本參數(shù)。反應(yīng)物濃度的變化率可以用表征組分濃度等值面的相對移動(dòng)速度以及組分的擴(kuò)散項(xiàng)來表示。
使用的湍流燃燒模型中,湍流燃燒傳播速度的賦值是使用湍流褶皺修正因子乘層流火焰?zhèn)鞑ニ俣?。這個(gè)賦值方法的理論基礎(chǔ)是,湍流火焰?zhèn)鞑ニ俣鹊脑龃笾饕且驗(yàn)榛鹧婷嬖谕牧髁鲃?dòng)作用下呈現(xiàn)褶皺的狀態(tài),火焰面的褶皺增大了反應(yīng)面的面積,從而增大了湍流火焰的傳播速度,但湍流火焰?zhèn)鞑ニ俣鹊幕A(chǔ)仍然是火焰固有的層流火焰?zhèn)鞑ニ俣?。湍流尺度量的獲得,從流動(dòng)控制方程的求解中可以得到。而火焰的基礎(chǔ)性參數(shù)如層流火焰?zhèn)鞑ニ俣?,火焰厚度等,則需要化學(xué)反應(yīng)動(dòng)力學(xué)模型求解才能得到。層流火焰?zhèn)鞑ニ俣?,火焰厚度可以使用化學(xué)反應(yīng)機(jī)理,輸運(yùn)參數(shù)建立一維平面火焰模型計(jì)算得到。該文章中使用Chemkin軟件中的Premix模塊來求解這些基礎(chǔ)性火焰參數(shù)[6]。
仿真模擬計(jì)算的求解參數(shù)包括初始溫度、熱邊界條件、流體域工況條件。圖2為安全殼模型及網(wǎng)格示意圖。安全殼結(jié)構(gòu)的初始溫度與內(nèi)流場初始溫度一致,為498K。安全殼的外部為空氣,空氣溫度為297.15K。安全殼的6個(gè)外壁面為自然對流邊界,對流換熱系數(shù)為10W/㎡K。安全殼內(nèi)氫氣爆燃爆轟的CFD模擬工況為88mm穩(wěn)壓波動(dòng)管工況,氫氣濃度為0.32、氧氣濃度為0.11、水蒸氣濃度為0.19、初始溫度493K、初始壓力為1.33MPa。
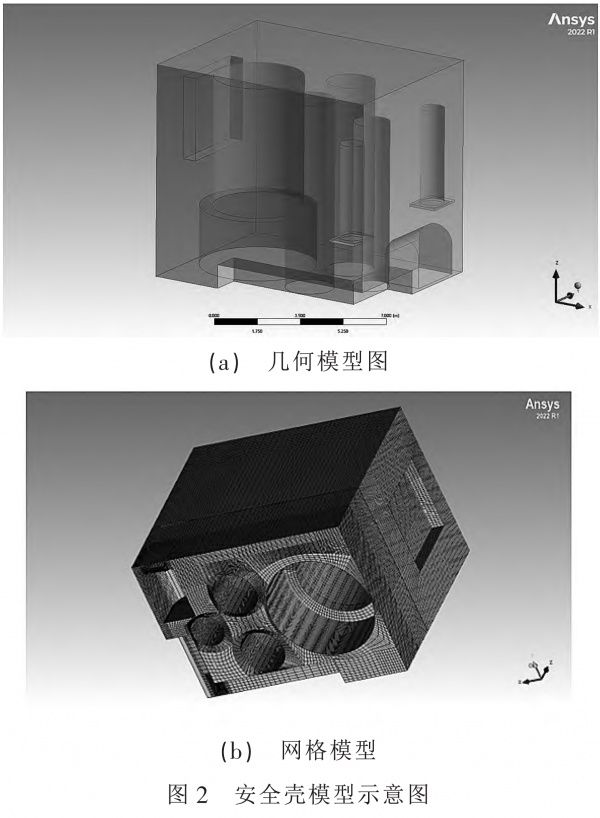
2模擬結(jié)果與討論
2.1流場模擬結(jié)果與討論
氫氣-空氣火焰的層流燃燒速率是湍流爆燃模型的一個(gè)重要輸入?yún)?shù)。在氫氣爆燃模擬計(jì)算中,使用的氫氣-空氣火焰的基礎(chǔ)參數(shù)包括層流燃燒速率(Laminar burning velocity,LBV),火焰厚度,火焰絕熱過程對應(yīng)的變化反應(yīng)級數(shù)[7]。這些基礎(chǔ)性參數(shù)的計(jì)算使用反應(yīng)動(dòng)力學(xué)軟件Chemkin完成。氫氣-空氣火焰的反應(yīng)機(jī)理使用國內(nèi)外廣泛使用的FFCM機(jī)理。由于罐體中爆燃火焰?zhèn)鞑τ谖慈紖^(qū)域的壓縮屬于絕熱壓縮過程,可以將氫氣-空氣火焰的層流燃燒速率和溫度、壓力的函數(shù)關(guān)聯(lián),表示為未燃區(qū)域壓力比的函數(shù)。
為了得到壓縮的未燃區(qū)域氫氣-空氣火焰對應(yīng)的層流燃燒速率,我們根據(jù)氫氣-空氣混合氣體的絕熱指數(shù),設(shè)置一系列初始壓力和溫度,進(jìn)而計(jì)算對應(yīng)的層流燃燒速率。將這一系列的壓縮的未燃區(qū)域氫氣-空氣層流燃燒速率擬合為5階的多項(xiàng)式函數(shù),即可在氫氣-空氣湍流爆燃模型中作為層流燃燒速率的輸入?yún)?shù)使用。該工況下壓縮的未燃區(qū)域氫氣-空氣根據(jù)FFCM反應(yīng)機(jī)理計(jì)算的層流燃燒速率結(jié)果以及擬合的5階多項(xiàng)式,而壓縮的未燃區(qū)域氫氣-空氣層流燃燒速率的計(jì)算擬合多項(xiàng)式并作為后續(xù)湍流爆燃模型的輸入?yún)?shù)。如圖3所示為氫氣-空氣火焰的層流燃燒速率圖,展示了不同壓力比下的氫氣空氣火焰層流燃燒速率。該工況初始壓力為1.33MPa,此時(shí)的空氣氫氣火焰層流燃燒速率為2.11m/s,且隨壓力比增加,空氣氫氣火焰層流燃燒速率減小。
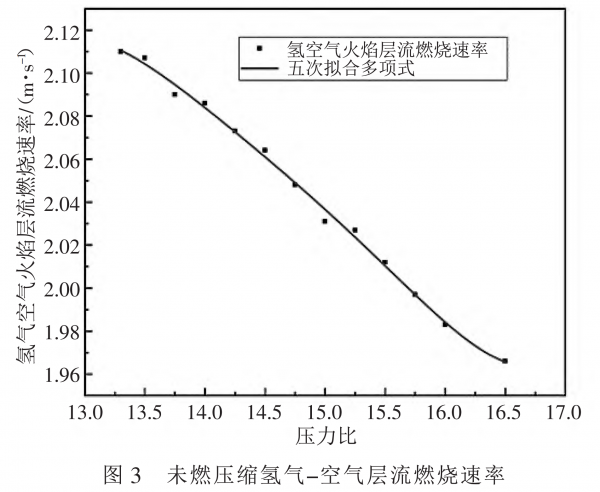
由于該工況下初始火焰層流傳播速度為2.11m/s,所以該工況爆燃發(fā)生后內(nèi)部流場傳播十分迅速。如圖4所示,在點(diǎn)火后0.12s時(shí),火焰鋒面在傳播過程中先到達(dá)安全殼四周壁面處,在0.18s時(shí),火焰鋒面到達(dá)安全殼頂部,在0.3s時(shí)刻,整個(gè)安全殼內(nèi)部溫度達(dá)到最大值,隨后由于壁面散熱,溫度逐漸開始下降,但是由于該工況爆燃十分劇烈,其溫度下降并不明顯。
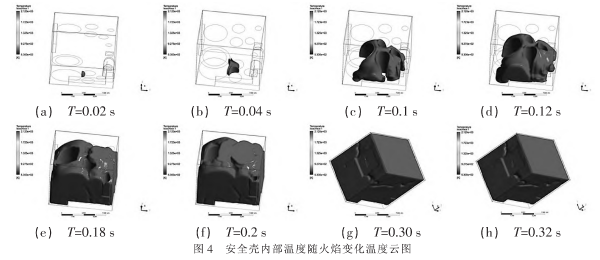
圖5分為3個(gè)階段:第一階段為0~0.1s,此時(shí)壓力變化很小,第二階段為0.1~0.25,該時(shí)間段壓力顯著增大,第三階段為0.25s之后,壓力開始緩慢下降,此時(shí)內(nèi)部已經(jīng)達(dá)到平衡狀態(tài)。結(jié)合不同時(shí)刻安全殼內(nèi)部溫度云圖可知,氫氣爆燃對應(yīng)的超壓變化大致分為3個(gè)階段。第一階段,火焰?zhèn)鞑フ紦?jù)的已燃區(qū)域尺度遠(yuǎn)小于安全殼的尺度,爆燃火焰的膨脹作用導(dǎo)致的封閉空間壓力升高很小,相應(yīng)的此時(shí)安全殼內(nèi)超壓值相比超壓峰值幾乎可以忽略,如爆燃火焰的尺度為安全殼尺度的10%,已燃區(qū)域體積占安全殼體積約為0.1%,此時(shí)超壓值約為初始壓力的0.3%,為超壓峰值的0.1%,在超壓曲線中幾乎分辨不出。第二階段,爆燃火焰占據(jù)的已燃區(qū)域尺度和安全殼尺度為同一個(gè)量級,此時(shí)已燃區(qū)域的氣體膨脹效應(yīng)會(huì)顯著影響封閉空間的壓力,相應(yīng)的安全殼內(nèi)的超壓值開始顯著增大,超壓增長率最大時(shí)刻即在第二階段。第三階段,爆燃火焰接觸安全殼頂部壁面,超壓值達(dá)到峰值,為0.75MPa,安全殼外壁的散熱導(dǎo)致安全殼內(nèi)氣體溫度逐漸降低,超壓值開始降低。

2.2安全殼完整性結(jié)果與討論
基于安全殼結(jié)構(gòu)熱力學(xué)特性仿真結(jié)果,給出0.03、0.18和0.39s時(shí)刻的安全殼溫度及熱通量分布如圖6所示。從圖中可以看出,安全殼結(jié)構(gòu)的最低溫度隨氫氣爆燃的時(shí)間增加而增大,從0.03s的198.73℃開始最終增大到0.39s的1512.8℃。0.3s之前,最低溫度的增長速率較小,而0.3s之后則急劇增加。隨著時(shí)間的增加,安全殼的最高溫度存在局部波動(dòng),但是整體上呈現(xiàn)出先增大后減小的變化趨勢,峰值溫度出現(xiàn)在0.18s的時(shí)刻,峰值為3959.9K。隨著時(shí)間的增加,熱流密度呈現(xiàn)出先增大后減小的變化趨勢,熱流密度先是從0.03s的812100W/㎡迅速增大到0.18s的峰值12565000W/㎡,而后逐漸減小,最終減小為0.39s的1414100W/㎡。熱流密度的最小值則整體上隨時(shí)間的增大而增大,但在0.30s和0.33s出現(xiàn)局部的減小情況。
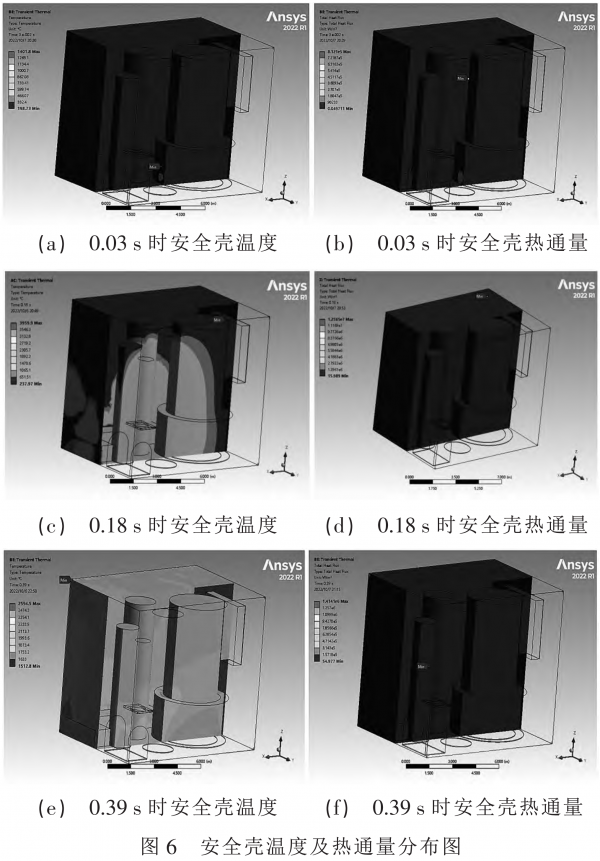
基于安全殼結(jié)構(gòu)動(dòng)力學(xué)特性仿真結(jié)果,給出0.03、0.18和0.39s時(shí)刻的安全殼變形位移及結(jié)構(gòu)應(yīng)力分布如圖7所示。從圖中可以看出,由于底面施加了固定約束,底面的位移為0m。安全殼結(jié)構(gòu)的最大變形隨時(shí)間的增加而增大,0.39s時(shí)刻最大變形量為95.274m,可知安全殼結(jié)構(gòu)已經(jīng)發(fā)生了塑性變形,安全殼結(jié)構(gòu)已經(jīng)遭到結(jié)構(gòu)性破壞。隨著時(shí)間的增加,安全殼的結(jié)構(gòu)應(yīng)力的極大值整體呈現(xiàn)增大變化趨勢,最大應(yīng)力出現(xiàn)在0.39s時(shí)刻,約為2.6E+11Pa??紤]到結(jié)構(gòu)鋼的屈服強(qiáng)度為235MPa,可知安全殼的最大應(yīng)力遠(yuǎn)大于材料的屈服極限,安全殼發(fā)生了塑性變形,結(jié)構(gòu)遭到破壞。
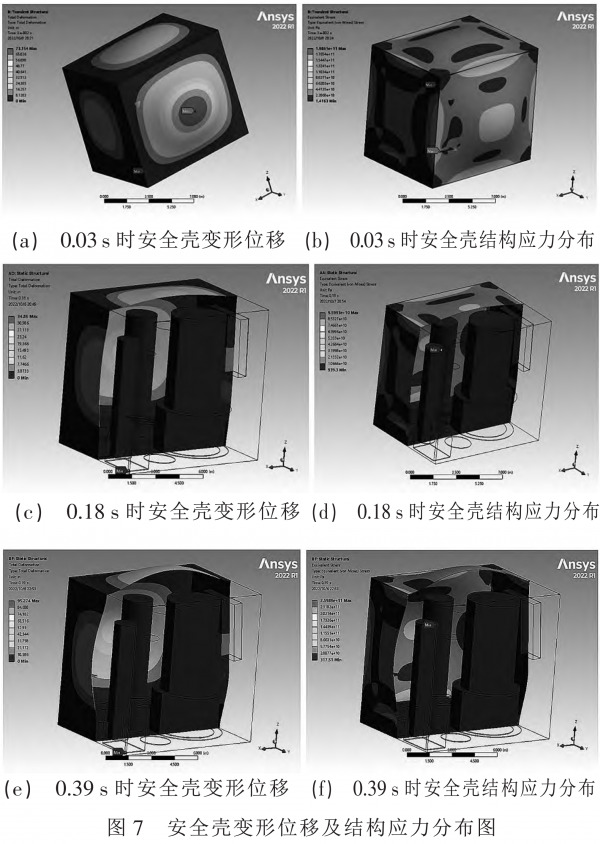
3結(jié)論
文章主要針對氫氣爆燃條件下安全性進(jìn)行仿真研究,通過對安全殼內(nèi)部氫氣爆燃事故工況下爆燃條件進(jìn)行數(shù)值模擬仿真計(jì)算,得到如下結(jié)論。
1)安全殼內(nèi)氫氣等混合氣體被點(diǎn)燃后,呈現(xiàn)出球形火焰鋒面,并向外傳播,但由于安全殼的內(nèi)部有許多不規(guī)則形狀障礙物,火焰鋒面在傳播過程中的形狀逐漸偏離球形,其流動(dòng)也由紊流變?yōu)橥牧??;鹧嬖趥鞑ミ^程中會(huì)先傳至四周壁面,然后再頂部壁面,隨后充滿整個(gè)安全殼內(nèi)部,此時(shí)溫度達(dá)到最大,之后由于壁面散熱,整個(gè)安全殼內(nèi)部溫度趨近于平衡。
2)結(jié)合不同時(shí)刻安全殼內(nèi)部溫度云圖可知,氫氣爆燃對應(yīng)的超壓變化大致分為3個(gè)階段。第一階段,火焰?zhèn)鞑フ紦?jù)的已燃區(qū)域尺度遠(yuǎn)小于安全殼的尺度,爆燃火焰的膨脹作用導(dǎo)致的封閉空間壓力升高很小,相應(yīng)的此時(shí)安全殼內(nèi)超壓值相比超壓峰值幾乎可以忽略,例如爆燃火焰的尺度為安全殼尺度的10%,已燃區(qū)域體積占安全殼體積約為0.1%,此時(shí)超壓值約為初始壓力的0.3%,為超壓峰值的0.1%,在超壓曲線中幾乎分辨不出。第二階段,爆燃火焰占據(jù)的已燃區(qū)域尺度和安全殼尺度為同一個(gè)量級,此時(shí)已燃區(qū)域的氣體膨脹效應(yīng)會(huì)顯著影響封閉空間的壓力,相應(yīng)的安全殼內(nèi)的超壓值開始顯著增大,超壓增長率最大時(shí)刻即在第二階段。第三階段,爆燃火焰接觸安全殼壁面,超壓值達(dá)到峰值,安全殼外壁的散熱導(dǎo)致安全殼內(nèi)氣體溫度逐漸降低,超壓值開始降低。
3)在安全殼內(nèi)氫氣爆燃爆轟所產(chǎn)生高溫和高壓的影響下,安全殼結(jié)構(gòu)的最大變形為95.274m,最大應(yīng)力約為2.6E+11Pa,遠(yuǎn)大于安全殼所用結(jié)構(gòu)鋼材料的屈服極限,安全殼發(fā)生了塑性變形,結(jié)構(gòu)遭到根本性的破壞。
參考文獻(xiàn):
[1]袁璐,曹學(xué)武.核電廠嚴(yán)重事故下氫氣源項(xiàng)的不確定性分析[J].原子能科學(xué)技術(shù),2021,55(11):2036-2042.
[2]鄧堅(jiān).大型干式安全殼嚴(yán)重事故條件下氫氣控制研究[D].上海:上海交通大學(xué),2008.
[3]孫洪平,張弛.AP1000核電廠嚴(yán)重事故下氫氣安全分析[C]//中國核學(xué)會(huì)核能動(dòng)力分會(huì)反應(yīng)堆熱工流體專業(yè)委員會(huì),中核核反應(yīng)堆熱工水力技術(shù)重點(diǎn)實(shí)驗(yàn)室.第十五屆全國反應(yīng)堆熱工流體學(xué)術(shù)會(huì)議暨中核核反應(yīng)堆熱工水力技術(shù)重點(diǎn)實(shí)驗(yàn)室學(xué)術(shù)年會(huì)論文集.西安交通大學(xué)核科學(xué)與核技術(shù)學(xué)院;環(huán)境保護(hù)部核與輻射安全中心,2017:10.
[4]韓剛,郭美榮,劉瑞.基于ANSYSWorkbench的雙向流固耦合振動(dòng)仿真方法[J].齊齊哈爾大學(xué)學(xué)報(bào)(自然科學(xué)版),2023,39(6):11-14.
[5]孫楠.CH4在O2/CO2氣氛下預(yù)混火焰特性的數(shù)值模擬[D].沈陽:東北大學(xué),2015.
[6]朱睿.摻混氫氣對甲烷/空氣一維層流火焰的影響[J].節(jié)能,2022,41(8):62-65.
[7]劉海清,張林瑤,邢暢,等.氫燃料特性及氫微混火焰模式分析[J/OL].中國電機(jī)工程學(xué)報(bào),1-11[2024-06-20].https://doi.org/10.13334/j.0258-8013.pcsee.232125. |